| |
Section K (26/12/08
)
FUEL SYSTEM
K.1 General
K.2 Removal of the fuel tank
K.3 Removal of the fuel gauge float unit
K.4 Removal of the filter tube assembly
K.5 Removal of the fuel strainer
K.6 The fuel pump
K.7 Air cleaner
K.8 The carburettor (Stage I)
K.9 Description and operation
K.10 Carburettor adjustments
K.11 Overhauling the carburettor
K.12 The carburettor (Stage II)
K.13 Tuning and fitting instructions
K.14 Specifications and repair data
|
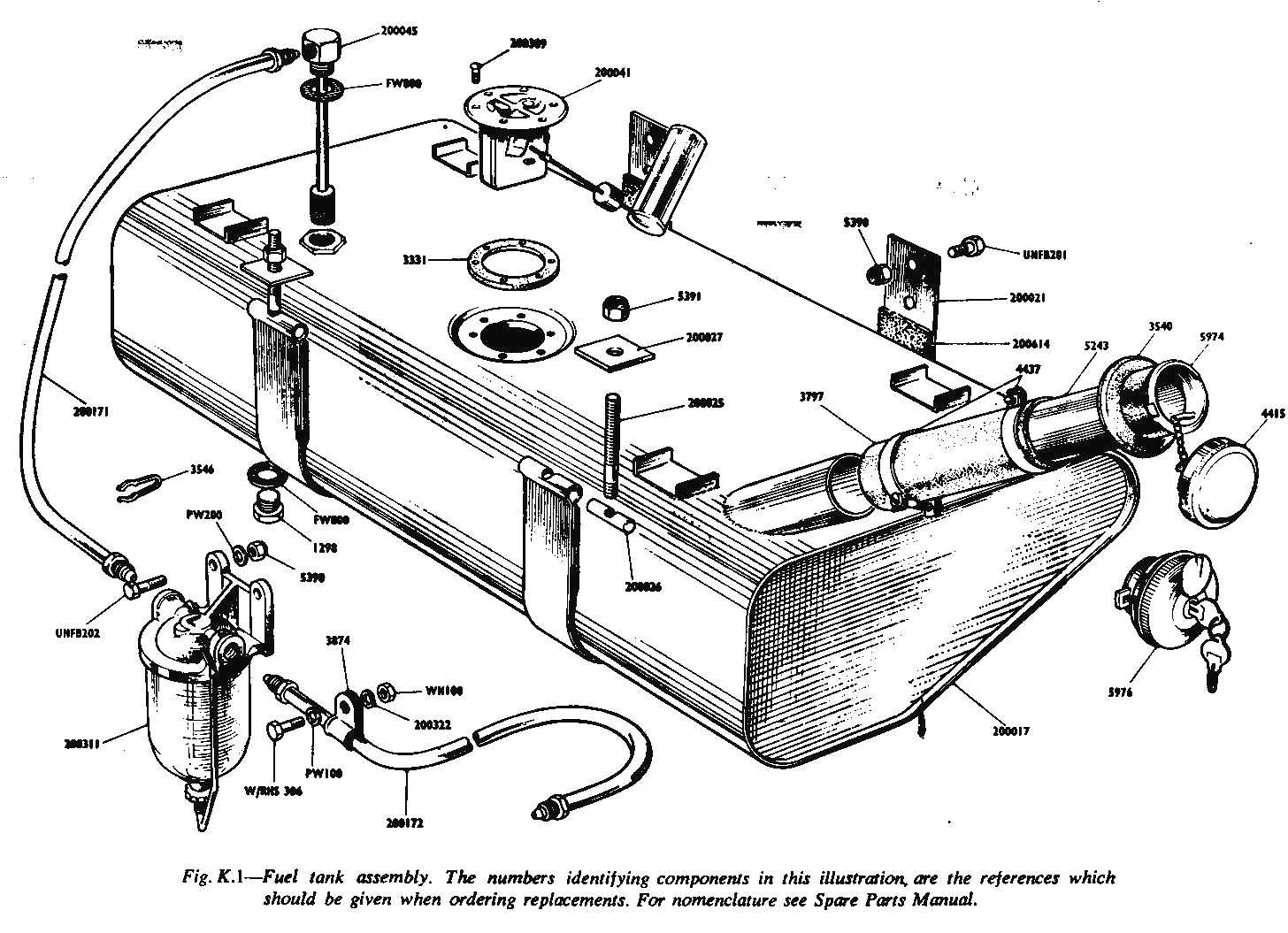
|
|
|
|
Kl
The 81/2 gallon capacity fuel tank is situated at the
rear of the chassis and is secured by straps to the rear of the chassis
underside. Delivery of the fuel is effected by a mechanically driven pump
drawing fuel from the tank through a filter tube assembly and flexible
nylon pipe to a petrol strainer mounted on the engine bulkhead. Fuel
content is measured by a float-operated variable resistance located in a
well on the tank upper surface; the resistance is transmitted to the fuel
contents gauge mounted on the facia panel.
K2
Removal of the Fuel Tank
Jack up the vehicle and drain off petrol at drain plug.
Disconnect tank inlet pipe from flexible hose by removing Jubilea clips
and disconnect fuel gauge wiring at the float unit; access to these items
is through the luggage boot, a small inspection plate being removed to
expose the float unit beneath. Unscrew the two nuts securing the strap
trunnions to the chassis cross member, collect the nuts and two retaining
plates. When the tank is removed, the straps can be left attached by their
bolts and nuts to the rear chassis cross member.
To refit or renew a tank, reverse the above operations.
When refitting ensure that the felt packing is in position between the
tank and chassis frame and between the tank and the straps. After the tank
has been positioned, strap adjustment is taken up on the strap trunnions.
When refitting the drain plug, ensure that the fibre washer is clean and
undamaged.
K3
Removal of the Fuel Gauge Float
Unit
With the fuel gauge electrical wiring previously
disconnected, remove six retaining screws and lift out float unit with
cork gasket. Care must be exercised not to bend or strain the float lever
or dent the float. When refitting the float unit, check that the cork
gasket is clean and undamaged prior to coating with jointing compound.
Position the float unit in the tank and secure with six screws ensuring
that the joint between the tank and the fuel unit is fuel tight.
K4
Removal of the Filter Tube
Assembly
Unscrew assembly from the tank, exercising care with
filter end to prevent damage. Collect flbre washer. When refitting the
assembly ensure that the fibre washer is clean and undamaged. Tighten down
and secure to ensure a fuel tight joint. |
|
K5
Removal of the Fuel Strainer
Disconnect fuel pipes from the tank and fuel pump at
the fuel strainer, with nine fixing clips to the right hand side of the
chassis.
NOTE: Whenever fuel pipes are disconnected, the ends
must be sealed to prevent the ingress of dirt or moisture.
K6
THE FUEL PUMP
The fuel pump is mounted on the right hand side of the
engine, adjacent to the oil filter, and is driven by means of a rocker arm
from an eccentric on the camshaft.
Operation of the Fuel Pump
On rotation of the engine, the eccentric on the
camshaft pivots the fuel pump rocker arm and link, and pulls the diaphragm
downwards against the pressure of the return spring. This creates a
partial vacuum in the pump chamber, causing the inlet valve to open and
draw fuel from the tank through the pipe line and the glass sediment bowl.
Any sediment in the fuel is deposited in the glass bowl, being filtered by
the gauze in the top of the sediment bowl before passing on to the fuel
pump.
Further movement of the camshaft eccentric allows the rocker arm to
return and the diaphragm is pushed up by the return spring, causing the
inlet valve to open. The fuel is then forced through the pump to the
carburettor (or car- burettors in the case of the Stage II version). When
the fuel in the carburettor bowl raises the float sufficiently to close
the needle valve, a back pressure is created in the pump charnber, which
prevents the diaphragm being pushed up by the return spring, until the
needle valve opens again.
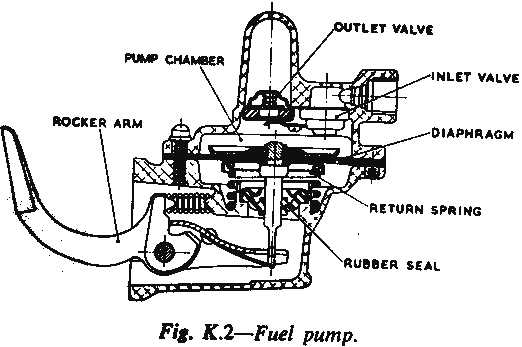
|
|
|
|
During the time that the diaphragm is held down by fuel
pressure, the rocker arm idles on the eccentric without operating the
link.
Cleaning the Fuel Filter Screen
The glass sediment bowl and filter (mounted on the
front bulkhead, Left Hand Drive only) should be removed and washed in
petrol every 5,000 miles (8,000 km.).
To Remove and Replace
1. Slacken off the clamp screw at the base of the
sediment bowl, move the retainer clip aside and detach bowl, filter screen
and cover gasket.
2. When replacing the filter screen, ensure that it
seats in its housing correctly, and also that the cover gasket fitted
between the sediment bowl and the body is in good condition, as an air
leak at this point may cause failure of the fuel supply. If in doubt, fit
a new cover gasket and tighten the clamp screw securely.
3. Complete removal of the sediment bowl can be
effected by the removal of the two bolts and Oddie nuts securing the bowl
to the bulkhead.
NOTE : There is no sediment bowl on the R.H. Drive car
and the fuel supply is fed direct from the tank to the AC fuel pump.
Testing the Fuel Pump
Provided there are no air leaks or obstructions in the
fuel lines, a quick check on the pump can be made, as follows:
1. Disconnect the fuel pump from the carburettor pipe
at the pump outlet or the carburettor union.
2. Crank the engine, using the starter motor, when
there should be a well-defined surge of fuel for each revolution of the
camshaft. If the pump does not operate correctly, check the inlet
depression and delivery pressure, using suitable gauges.
Fuel Pump Inlet Depression Test
1. Fill the float chamber with petrol.
2. Disconnect the fuel pump flexible pipe from the pump
inlet and connect a vacuum gauge to the inlet union.
3. Start the engine and allow it to run at an idling
speed, when the vacuum reading should be at least 10 in. (25,4 cm.) of
mercury.
4. Stop the engine, when the gauge needle should take
at least one minute to drop back to zero.
Fuel Pump Delivery Pressure Test
1. Fill the float chamber with petrol.
2. Disconnect the fuel pump to carburettor pipe and
connect the pressure gauge to the pump outlet.
|
|
3. Start the engine and observe the pressure when
running at idling speed. Momentarily race the engine and observe the
pressure. This should not be less than 11 lb./sq. in. (0,10 kg./sq. cm.)
and not more than 3 lb./sq. in. (0,21 kg./sq. cm.) at any speed.
Fuel Pump Removal and Replacement
To remove:
1.
Disconnect the fuel inlet and outlet pipes.
2.
Unscrew the two nuts securing the pump to the cylinder block and
detach the pump.
3.
Remove pump gasket.
To
replace :
1.
Locate new gasket on pump mounting flange studs.
2.
Refit the pump to the cylinder block studs, passing the rocker arm
up between the camshaft eccentric and the wall of the crank case. Replace
the two securing nuts and spring washers and tighten to 12 -> 15 Ib. ft.
(1,66 -> 2,07 kg. nm.).
3.
Reconnect the fuel inlet and outlet pipes to their respective
unions on the pump and tighten securely.
K7
AIR CLEANER
To carry out normal servicing, remove the three
securing bolts and one nut. The cleaner can then be removed from the car.
Unscrew the, filter bowl, empty out the old oil, clean out thoroughly and
refill with fresh oil to the indicated level. Reassemble and fit to the
carburettor. 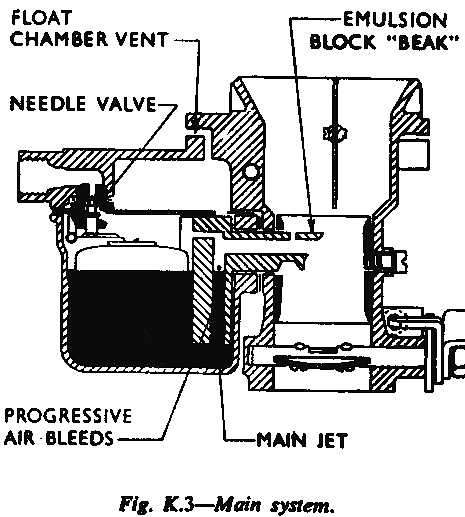
|
|
|
|
K8
THE CARBURETTOR (STAGE I)
The Stage I carburettor is of the single-venturi
vertical downdraught type. It incorporates an accelerator pump to ensure
rapid acceleration, an economy device controlled by manifold depression is
incorporated in the carburettor body to improve petrol consumption at
higher speeds, and a choke valve of the strangler type for cold
starting.
K9
DESCRIPTION AND OPERATION
-
Starting
System
A rich mixture is required for starting. The choke valve is
shut by means of the instrument panel control; the carburettor linkage
partially opens the throttle plate. As the engine is rotated by the
starter motor, a high depression is created upon the emulsion block
discharge beak, see Fig. 3, and fuel is thus drawn from the capacity
well in the emulsion block. When the engine is running with the choke
shut, the depression created in the manifold at low speed causes the
spring-loaded choke plate, which is offset on its spindle, to open,
thereby admitting sufficient air to keep the engine running.
-
Idling
System (see Fig. 4)
When the throttle plate is in the idling position,
the fuel is supplied by the slow running jet. This jet is fed through
a passage from the metered side of the main jet which is located at
the base of the emulsion block. The fuel is emulsified by air admitted
through the air bleed hole in the main air intake and the bleed hole
positioned immediately above the idling jet. The resulting mixture is
drawn down the vertical channel in the carburettor body to the idling
discharge hole just below the throttle plate, and thence into the
induction manifold. The quantity of mixture passing through the idling
discharge hole is regulated by the needle-type volume control screw.
(See Carburettor Adjustment). The small hole in the carburettor body
above the idling discharge hole also communicathes with the supply
channel and serves to provide a smooth and progressive supply of
mixture as the throttle plate is gradually opened.
-
Main System (see Fig. 3)
As the throttle plate
continues to open, the engine depression at the emulsion block beak draws
fuel from the capacity well in the emulsion block and the channels above
the main and compensating jets. At the same time, air is admitted by the
'full throttle' air bleed (which remains permanently open) and also, if
operative, by the 'part throttle' air bleed which is controlled by the
economy diaphragm valve, see Fig. 4. The resulting mixture of fuel and air
is drawn from the emulsion block beak into the induction manifold.
|
|
As the petrol level in the main jet channel falls, a
number of small holes in the side of the channel are progressively
exposed, see Figs. 3 and 4. This admits an increasing quantity of air into
the system, thus maintaining the correctly balanced fuell-air ratio of the
mixture.
Economy Device (see Fig. 4)
At the side of the carburettor body is a small casting
attached by three screws. Inside is a diaphragm valve, which is normally
held in a flexed condition by a compression spring. From the spring
compartiment a small drilling gives direct communication with the engine
side of the throttle plate through internal channels.
Under 'part-throttle' cruising conditions, the manifold
depression is high. This depresssion is imposed on the spring-loaded side
of the diaphragm, thereby lifting the valve from its seat and so
increasing the ventilation via the 'part-throttle' air bleed to the jets,
thus weakening the mixture.
When the depression in the manifold is low, the valve
remains on its seating under the influence of the spring. The air supply
to the jets is consequently limited to the permanent restriction of the
'full throttle' air bleed. The action of the economy device is entirely
automatic
and is controlled by the demands of the engine.
Accelerator Pump System (see Fig. 5)
The purpose of the accelerator pump is to prevent any
hesitation when suddenly accelerating by providing a controlled and
metered supply of fuel into the carburettor venturi coincident with the
sudden opening of the throttle plate.
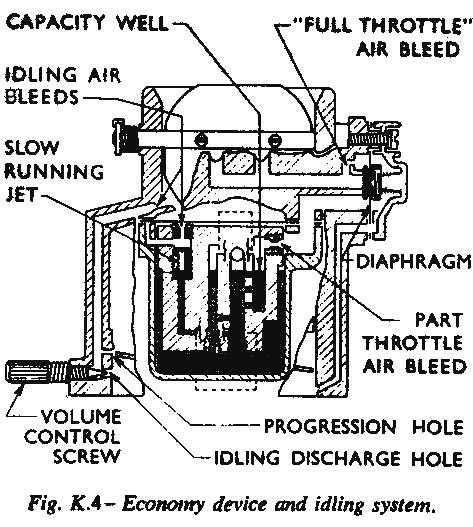
|
|
|
|
When the pump piston is at the top of its stroke, the
pump chamber is charged with fuel admitted from the float chamber through
the non-return valve at the base of the chamber. When the throttle is
suddenly opened, the piston is forced down by the throttle linkage and
discharges a stream of petrol through the nonreturn valve located at the
top of the float chamber body, and through the horizontal discharge nozzle
into the main air stream. The pump piston is returned to the charged
position by the piston spring and is then ready for the next stroke. The
travel of the piston, and consequently, the volume of fuel discharged at
each stroke can be set in one of two positions. (See 'Carburettor
Adjustments.")
K10
CARBURETTOR ADJUSTMENTS
(a) Slow Running Adjustment (see Fig. 6)
To obtain the best slow running adjustment, the engine should be tuned
against a vacuum gauge connected to the inlet manifold at the point where
the connection is taken for the vacuum pump. Before commencing adjustment,
check the air cleaner to ensure that the element is clean and, in the case
of the oil bath cleaner, that the oil is clean and at the correct level.
Run the engine to allow it to warm up. To adjust the slow running, screw
in the throttle stop screw until a fast idling speed is obtained, then
turn the volume control screw either clockwise or anti-clockwise to obtain
the maximum vacuum reading. Readjust the idling speed as necessary, and
continue the adjustment until the maximum possible vacuum reading is
obtained with a reasonable slow running speed. |
|
When a suitable vacuum gauge is not available, the
engine should be warmed up and the throttle stop screw turned clockwise so
that the engine is running at a fast idling speed. Screw the volume
control screw in or out until the engine runs evenly. Now readjust the
throttle stop screw if the engine is running too fast, followed by a
further readjustment of the volume control screw. These operations should
be repeated until the idling speed is satisfactory. It may be necessary to
readjust the ignition setting.
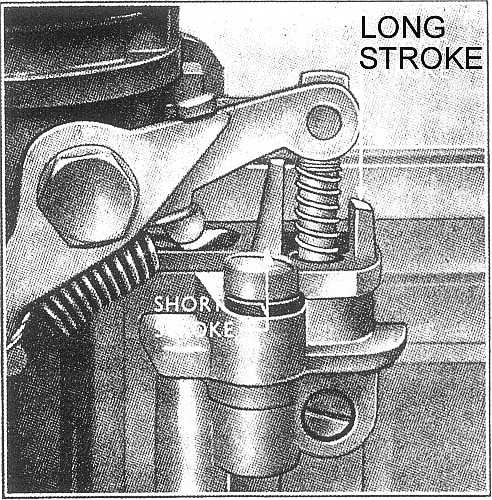
|
|
|
|
(b) Accelerator Pump Stroke Adjustment
The accelerator pump stroke can be adjusted by altering the position of
the stop fitted under the operating arm in the top of the float chamber.
In warm or temperate climates set the stop so that the operating arm will
contact the large boss to give a short pump stroke. In cold climates set
the stop so that the arm contacts the small boss allowing a long pump
stroke. To adjust the stop, lift it clear of the float chamber against the
tension of the spring and turn it through 180° (sec Fig. 7).
A felt seal is incorporated in the top carburettor body
below the adjusting collar.
(c) Choke Adjustments
The choke control cable is adjusted at the choke lever
plate trunnion so that there is approximately 1 in. (3,18 mm.) free play
in the cable when the control is pusbed in fully. The correct degree of
throtthe opening when the choke plate is closed for starting is obtained
by placing a 0,914 mm. drill (No. 64) between the edge of the throttle
plate and the carburettor body at right angles to the throttle spindle.
This setting can alternatively be obtained by screwing in the throttle
stop screw approximately six turns from the position at which it just
abuts the throttle plate stop when the throttle is fully closed (it will
be necessary to remove the throttle stop screw spring for making this
adjustment as the spring becomes 'coil-bound'). Then adjust the length of
the choke link so that the choke lever plate is in the fully closed
position.
|
|
(d) Float Adjustment
To check the fuel level it is necessary to remove the
float chamber. Operate the starter motor (ignition off) to fill the float
chamber to its correct level. Remove the four bolts securing the float
chamber to the carburettor body and carefully detach the float chamber.
With the float in position the petrol level should be 7/8 in. (22,5 mm.)
below the top face of the float chamber. If the float is removed, the
petrol level will fall and should then be 1-5/16 in. (33 mm.) below the
top face.
If the petrol level is low the float arm should be bent upwards
or bent downwards if the level is too high.
After adjusting the float arm, refit the float chamber and re-check
the petrol level as before.
K11
OVERHAULING THE CARBURETTOR
To Remove
1.
Remove the air cleaner.
2.
Disconnect the choke control cable at the choke lever plate and
slacken the clamp on the choke cable abutment bracket.
3.
Disconnect the throttle at the upper end of the throttle lever
connecting rod.
4.
Unscrew the fuel pipe union.
5.
Disconnect the distributor vacuum pipe at the rubber connection on
the right-hand side of the carburettor.
6.
Unscrew the carburettor flange nuts and spring washers and remove
the carburettor.
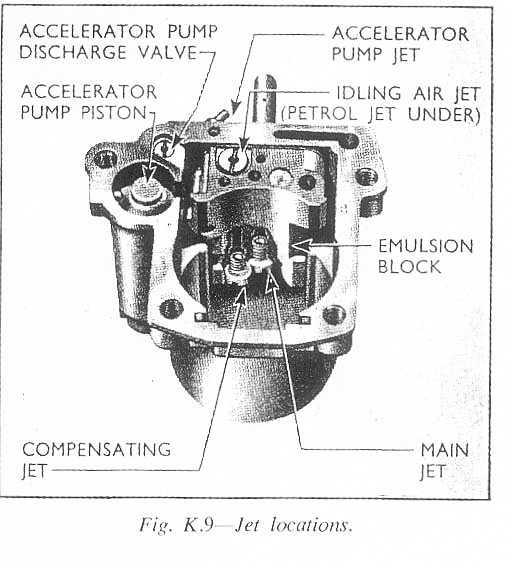
|
|
|
|
To Dismantle
-
Unscrew
the four bolts retaining the float chamber to the carburettor body and
detach the float chamber.
-
Release
the grub screw securing the connecting link between the choke valve
control lever and throttle spindle. Unscrew the bolt securing the
choke valve control lever to the carburettor body and detach the lever
and spring. Remove the screw and lockwasher retaining the choke cable
abutment bracket to the carburettor body.
-
Unscrew
the nut and lockwasher securing the throttle lever to the spindle,
pull off the throttle lever, accelerator pump operating lever, and
idling lever.
-
Remove
the pivot holt from the accelerator pump operating lever and detach
the two halves of the lever and the connecting spring link. Note that
a flat washer is fitted on each side of the operating lever. Pull the
accelerator pump adjustment stop out of the top of the float chamber.
-
Unscrew
the three bolts securing the economy valve housing to the carburettor
body. Remove the housing, spring and diaphragm assembly. Note that
gaskets are fitted on each side of the diaphragm assembly.
-
Unscrew
the needle valve and its metal seating washer from the carburettor
body.
-
Remove
the two screws retaining the choke valve to the spindle, withdraw the
spindle and detach the return spring.
-
Remove
the two screws securing the butterfly to the spindle, pull out the
butterfly and withdraw the spindle.
-
Straighten
the tab of the locking washer under the head of the choke tube
retaining screw, remove the screw and detach the choke tube.
-
Remove
the float hinge bracket and float from the float chamber, unscrew the
two bolts securing the emulsion block to the float chamber and detach
the emulsion block (see Fig. 8) The following jets are mounted in the
emulsion block and can be removed by unscrewing: the main jet,
compensating jet, compensating well air correction jet, idling petrol
jet and idling air correction jet (see Fig. 9).
Remove the screw retaining the accelerator pump operating plunger and
withdraw the plunger and spring. The accelerator pump inlet valve
assembly can be removed from the bottom of the well after removal of
the plunger and spring. Remove the accelerator pump outlet ball valve
and unscrew the discharge jet from the face of the float
chamber.
To
Reassemble
1.
Refit the choke tube and secure it in place with the retaining
screw. Ensure the end of the screw correctly locates in the hole in the
choke tube, fully tighten the screw and bend one tab of the lockwasher to
retain it in position. |
|
-
Fix
the throttle spindle in position so that the large flat faces towards
the mixture control screw. Refit the butterfly, securing it in place
with the two retaining screws. Fully tighten the screws and lightly
centre punch the ends of the screws to retain them in position. Fit
the choke valve spindle in position and ensure that one end of the
operating spring locates in the carburettor body and the other end
locates in the operating arm. Fit the choke valve in position with the
larger offset portion towards the carburettor and fit the two
retaining screws. Fully tighten the retaining screws and lightly
centre punch the ends of the screws to lock them in position.
-
Fit
the seating washer to the needle valve and screw the needle valve into
the carburettor body.
-
Replace
the economy valve assembly, checking that the valve seat is in good
condition. Carefully check the diaphragms to ensure that they are not
porous and locate the gasket on either side of the diaphragms with the
holes in line. Position the assembly on the carburettor body, locate
the diaphragm spring in the valve housing and secure the assembly to
the carburettor with three screws.
-
Fit
the accelerator pump adjustment stop to the carburettor body, locate a
flat washer on either side of the accelerator pump operating levers
and secure the assembly to the carburettor body with the pivot
bolt.
-
Locate
the choke control cable abutment bracket on the dowel of the
carburettor body and secure it in place with a screw and flat washer.
Locate the retracting spring on the boss on the choke operating lever
and secure the lever to the carburettor with a hexagonheaded bolt.
Ensure that the inner end of the retracting spring is located beneath
the abutment bracket and the outer end against the lower leg of the
operating lever.
-
Fit
the idling lever to the throttle spindle, screw the accelerator pump
operating lever on to the connecting link and locate the lever on the
throttle spindle. Fit the throttle lever to the spindle and secure it
in place with a lockwasher and nut.
-
Fit
the connecting link between the idling lever and choke control lever,
fit the choke control in the closed position and connect the link so
that in this position the butterfly is slightly open.
-
Fit
the accelerator pump inlet valve to the bottom of the operating
cylinder, locate the operating spring inside the operating plunger and
fit the plunger in position, securing it in place with the retaining
screw. Screw the accelerator pump outlet ball valve assembly into the
float chamber and the accelerator pump discharge nozzle into the face
of the float chamber
-
Refit
the jets to the emulsion block, locate a gasket on the front face of
the emulsion block and secure it to the inside of the float chamber
with two screws. Refit the float and hinge bracket. Refit the float
chamber to the carburettor body securing it in place with four
bolts.
|
|
|
|
To
Replace
1.
Locate a new gasket on the manifold flange and replace the
carburettor with the float chamber to the front. Refit the spring washers
and nuts on the mounting studs and tighten them securely.
2.
Reconnect the distributor vacuum pipe to the rubber connection on
the right-hand side of the carburettor.
3.
Refit the fuel pump pipe and tighten the union.
4.
Refit the throttle control rod to the upper end of the throttle
lever connecting rod.
5.
Connect the choke control cable (at the rear of the carburettor)
and tighten the clamp. Pass the cable inner wire through the choke lever
plate trunnion and tighten the clamping screw. Check that the choke opens
and closes correctly, and that there is slight play in the cable.
6.
Refit the air cleaner.
K12
THE
CARBURETTORS (STAGE II)
Conversion
to give Stage II performance can be effected, calling for the substitution
of twin S.U. Carburettors for the Single Zenith downdraught unit.
K13
TUNING
Fitting
Instructions (Twin Carburettor Assembly)
-
Disconnect throttle and choke at carburettor.
-
Remove existing carburettor complete with manifold.
-
Fit the two special studs provided in the two upper threaded holes
of inlet flanges on the cylinder head.
-
Fit the new inlet assembly using the new flange gaskets
provided.
-
Fit the two exhaust manifold retaining clips provided in place of
the original hot spot casting.
-
Remove the small brass 1/8 in. gas plug from the original manifold
and refit into new manifold.
-
Cut original fuel pipe in a position determined by the length of
pipe provided with new assembly and connect with rubber fuel pipe
provided.
-
On R.H.D. models, it is necessary to lengthen the throttle arm
protruding from the bulkhead by approximately 3 in. For this purpose an
extension is provided in the kit and this must be brazed or welded to the
existing arm. On L.H.D. models this is not necessary.
|
|
-
Connect up the throttle using the threaded rod and
ball ends
provided, after having cut the rod to a length suitable for correct
operation of the throttle, depending upon whether the vehicle is Left or
Right Hand Drive.
-
Ensure that full throttle can be obtained and that it also returns
to fully closed position. Connect up choke control. Tappet and ignition
settings are as standard.
The
S.U. carburettors are of the automatically expanding choke type, in which
the size of the choke and the effective area of the jet vary according to
the degree of throttle opening used against the prevailing load. This
regulation of the choke size gives a fairly constant air velocity over the
jet and ensures good atomisation, therefore multi-jets are unnecessary. The single jet used is varied in effective area by a tapered
needle which moves up and down in the jet orifice. The profile of the
needle is decided to suit each type of engine and running conditions.
Multi-carburettor installations cannot be successfully tuned unless the
general condition of the engine. i.c., compression, ignition system. are
in a satisfactory state.
With
regard to the carburettors themselves, the cleanliness of the section
piston units, the position of needles, the jet centering and oil level in
the dampers should be checked. The following sequence of tuning should be
followed:
-
Remove the air cleaners and run the engine until the normal
operating temperature is
reached.
-
Slacken one of the clamping bolts on the throttle spin idle
connections (1) Fig. 11 so that the throttles may be set independently.
-
Ensure that the throttle adjusting screws (2) Fig. 11 are holding
the throttles slightly open, about one-and-a- half turns from being clear
of the abutments. Disconnect the mixture control rod (1) Fig. 10.
-
The choke control screw (4) Fig. 11 should be clear of its
abutment and the choke cable disconnected if it is likely to interfere
with adjustment.
-
Set the engine idling speed to about 500 r.p.m. and using a length
of rubber tube about 1 ft. long and 1 in. bore as a stethoscope, check the
hiss of air at the carburettor intakes. They should be equal in volume, if
not proceed as follows:
-
With a downward pressure on the throttle adjusting screw (2) Fig.
11 adjust each intake until the 'hiss' is equal and the speed is 500
r.p.m. To reduce 'hiss' unscrew the adjusting screw.
-
When the desired condition has been achieved, stop the engine and
tighten the throttle spindle clamping screw and re-check.
-
Re-start the engine and allow it to idle at approximately 500
r.p.m.
|
|
|
|
-
Check the mixture strength by lifting the piston off the front
carburettor using the lifting pin (2) Fig. 10 approx. 1/32 in. (1,75mm)
when:
a.
If the engine speed increases the mixture strength of the front
carburettor is too rich.
b.
If the engine speed immediately decreases the mixture is too weak.
c.
If the engine speed momentarily increases very slightly followed by
a fall off in speed, the mixture strength is correct.
-
Carry out a similar check on the rear carburettor, and if
adjustments to mixture strength are necessary this can be varied by
screwing or unscrewing the jet adjusting nuts (3) Fig. 10.
To enrich the mixture the nut should be screwed down, to weaken it
screw the nut up. During this
adjustment it is necessary to ensure that the jets (4) are pressed upwards
so that they are in contact with the adjusting nuts.
When the adjustments are satisfactorily completed the exhaust note
should be regular and even.
-
Re-make any connections wich may have been disturbed and replace
air filters.
|
|
Jet Centralising
When the piston (5) Fig. 10 is lifted by hand, with the
engine not running and the jet adjusting nut screwed up fully, it should
fall freely and come into contact with the jet bridge with a soft metallic
click.
If this does not happen, then repeat the test with the
jet in its fully lowered position. If the click is now audible and the
piston falls freely then the jet nut must be re-centralised with the
needle.
The jet nut which is clamped in position by the gland
nut (6) Fig. 10 is located in a clearance bore which permits a limited
amount of float when the gland nut is slackened. Therefore, it can be
moved until it is concentric with the jet needle, allowing the piston to
fall freely to its lower position. To re-centralise proceed as
follows:
1.
Remove the air filters.
2.
Remove the return springs (7) and pivot pins (8) (Fig. 10). Move
the linkage out of the way.
3.
Remove piston dampers (5) Fig. 11.
4.
Withdraw the jet (4) Fig. 10 and remove the adjusting nut (3) and
springs (9).
|
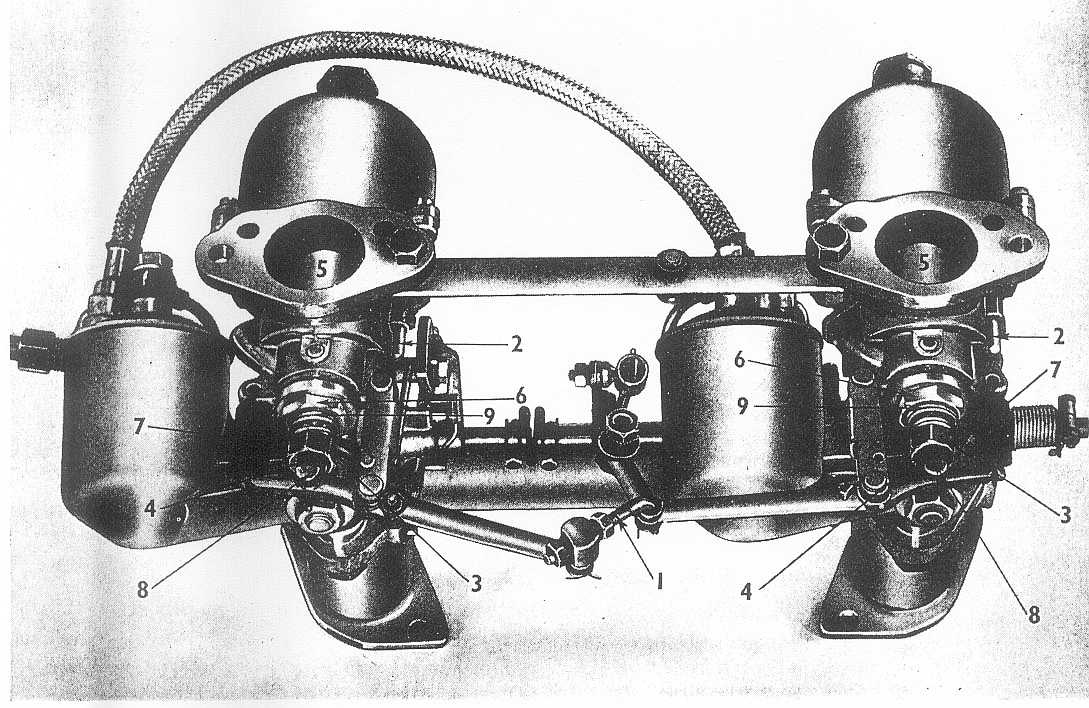 |
|
|
|
-
Replace the adjusting nut and screw it up to its upperrmost
position.
-
Slacken the gland nut and insert the jet.
-
Hold the jet in its upper position and move jet assembly laterally
until the jet is concentric with the needle, then tighten the gland nut.
When the correct condition is achieved, the piston assembly will fall
freely, hitting the jet bridge with a soft metallic click. Replace the
spring (g.), adjusting nut (3), jet (4), pivot pins, damper unit, etc. and
replenish the dash pots (5) Fig. 11 with oil of S.A.E.20 viscosity. The
oil level is correct when, using the damper as a dipstick, its threaded
portion is approximately 1 in. above the dash pots when resistance is
felt. The oil should be replenished, if necessary, every 3,000
miles.
Float
Chamber Fuel Level
The
level of the fuel in the float chamber is governed |
|
by the action of the forked lever in the float chamber
lid which acts upon the needle valve. The following procedure should be adopted if it is ever suspected that the fuel level is not correct.
1.
Disconnect the fuel pipe and remove the float chamber lid securing
bolt (3) Fig. 1 1. Lift off the lid.
2.
With the lid inverted and the forked lever resting on the needle
valve thus closing it, it should be possible to pass a 7/16 in. diameter
(11->112 mm.) rod between the radius of the forked lever and the float
chamber lid. If the forked lever fails to conform witbin 1/32 in. (0,7937
mm.) of the check figure, bend it carefully at the start of the fork
section, but take care to keep both prongs parallel with each other. There
should be no need to alter the fuel level unless flooding is experienced.
This can be caused by grit jamming the needle valve, a punctured float or
excessive engine vibration; these points should be checked first.
3.
Re-assemble. |
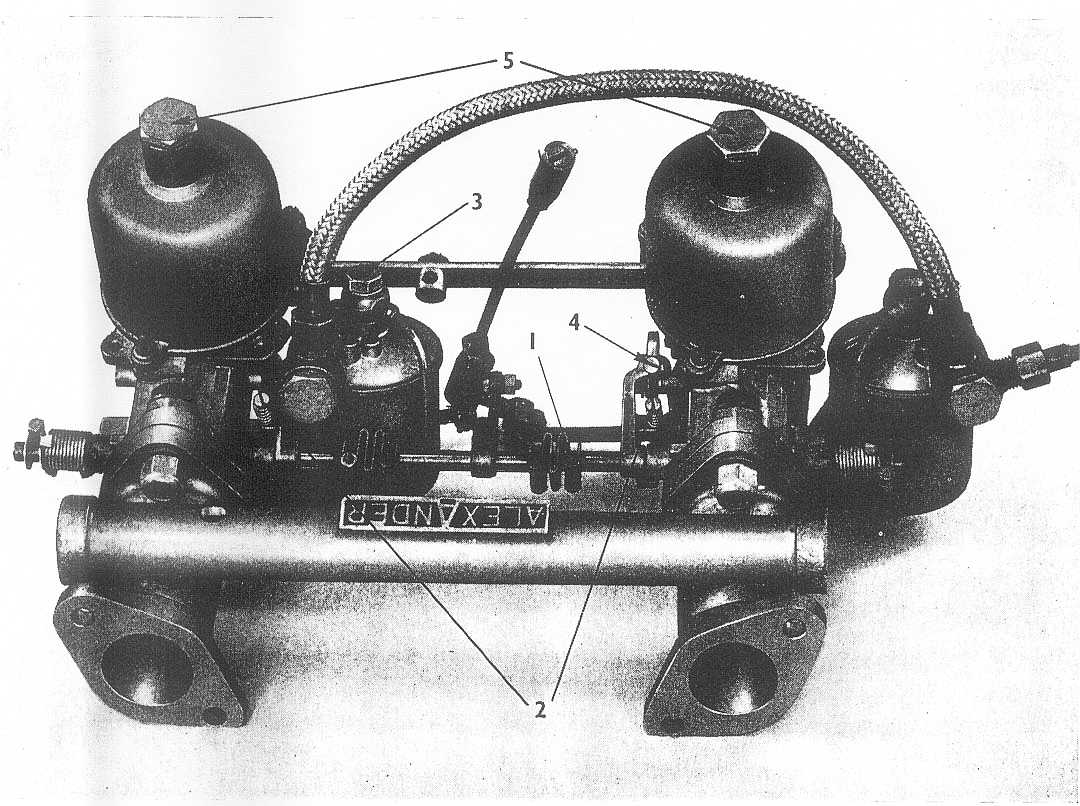 |
|
|
|
K14
SPECIFICATIONS AND REPAIR DATA
Fuel Tank Location... ... ... ... ... ... ..... ... ... ...
... At rear
of car, under luggage boot floor
Capacity... ... ... ... ... ... ... ... . ...
... ... 81 Imp. galls. approx. (10,2 U.S. galls., 45,4
litres)
Fuel Pump Type... ... ... ... ... . ... ... ..... ... .Diaphragm, operated by eccentric
on camshaft
Delivery Pressure... ... ... ... ... . ... ... ... 2 to 3-1/2 Ib/sq. in.
(140,6 to 246,05
gm/sq. cm.)
Inlet depression ... ... ... ... ..... . ... ... ... ...
... ... ... ... ... ...... ..10 in. (25,4 cm.) of
mercury
Fuel
Pump Diaphragm spring:
Test length... ... ... ... ... ... ...... . ... ... ... ... ... ... ... ... ...
... ... ... ... ...19/32 in. (15,081 min.)
Test load .. ... ... ... ... ... ... .. ..... ... ... ... ... ... ...
... ..104 to 112 oz. (2,949 to 3,175 kg. m.)
Rocker arm spring:
Test length ... ... ... ... ... ... .. ..... ... ... ... ... ... ... ...... ... ... ... ... ...
... 23/32 in. (18,256 mm.)
Test load ...
... ... ... ... ... ...... ... ... ... ... ... ... ... ... ... ...164 to 172 oz.
(4,65 to 4,88 kg. m.)
Carburettor (Stage I)
Type ...
... ... ... ... ... ... ... .. .... ... ... ... ... ... ... ... ... ...
... Zenith, single-venturi downdraught
Main jet ... ... ... ... ... ... ... .. ...
... ... ... ... ... ... ... ... ... ... ... ... ... .. . ... ... ... ...
... ...... ... ... 95
Main air bleed ... ... ... ... ... .. .. ...
... ... ... ... ... ... ... ... ... ... ... ... .. . ... ...
... ... ... ... 1,8 mm.
Idling jet ... ... ... ... ... ... ... .. ..
... ... ... ... ... ... ... ... ... ... ... ... ... ... ... ... ... ...
... ... ... ... ... 45
Compensating jet ... ... ... ... .. . ...
... ... ... ... ... ... ... ... ... ... ... ... ... . .. ... ... ... ...
... ... ... .105
Accelerator pump jet ... ... .. ...... ...
... ... ... ... ... ... ... ... ... ... ... ... ... ... ... ... ...
... ... ... ... 50
Idling jet air bleed ... ... ... ...... ..
... ... ... ... ... ... ... ... ... ... ... ... ... ... .. . ... ...
... ... ... ... ... 70
Choke tube diameter ... ... .. .... ... ...
... ... ... ... ... ... ... ... ... ... ... ... ... ... ... ... ... ...
... 28 mm.
Needle valve ... ... ... ... ... .. ...
... ... ... ... ... ... ... ... ... ... ..... ... ... ... ... ... ... ... ...
... . 1,75 mm.
Float chamber level:
Float in ... ... ... ... ... ... ...... ... ... ... ... ... ... ... ... ...
... ... ... ..7/8 in. (22,5 mm.) below top face
Float out ... ... ... ... ... .. ... ... ... ... ... ... ... ... ... ...
... ... ..1-5/16 in. (33,5 mm.) below top face
Carburettor (Stage II)
Type ... ... ... ..... ... ... ... ... ... ...
...... ... ... ... ... ... ... ... ... ... .. ... ... ... ... ... ...
Twin 1/2 H4 S.U.
Main
jet ... .. ... ... ... ... ... ... ... ... ... ... ... ... ... ... ... ....
... ... ... ... ... ... ... ... ... ... ... ... ... ... ...90
Needle
valve ... ... ... ... ...
... ... ... ... ... ... ... ... ... ... ...
... ..G.S.
Needle and red damper spring |
|
|
|
Common Technics
|